The Zilwaukee Bridge: From the Beginning
The following pages reproduce a 1987 report issued by the Michigan Department of Transportation in response to public concerns about the safety of the Zilwaukee Bridge, then nearing completion. The text here is reproduced word-for-word from the original report and no alterations—grammatical or otherwise—have been made. |
BRIDGE TECHNOLOGY
Technology for ost-tensioned, segmental, box girder bridges was developed in France and Germany in the late 1950s and early 1960s. Many have been built in western Europe and have been found to be generally more economical to build than steel bridges and less expensive to maintain because of corrosion concerns and painting costs with steel bridges.
The segmental bridge is built from individual concrete pieces, or segments, which are hollow and usually rectangular in shape. The segments are joined with post-tensioned steel cables to form the deck, or superstructure, of the bridge.
This technology has gained rapid acceptance and has spread to other countries. Today, there are more than 70 segmental bridges either completed or under construction in the United States and Canada. They range from a few hundred feet in length to the huge I-205 Freeway Bridge, spanning the Columbia River at the border of Washington and Oregon, opened in 1982, and the new Sunshine Skyway Bridge at Tampa, Fla., opened in 1987.
SEGMENTAL BRIDGE TYPES
Segmental bridges are in two general categories: precase and cast-in-place. Precast segments, such as those at the Zilwaukee Bridge, are fabricated in a specially built facility and then transported to the construction site. Cast-in-place bridge segments are cast in traveling forms placed directly on the bridge superstructure.
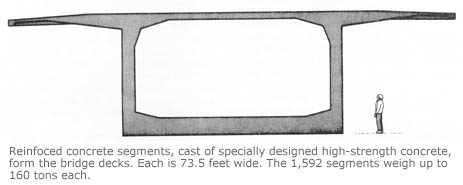
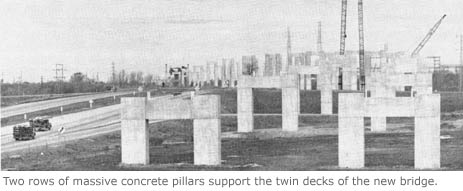
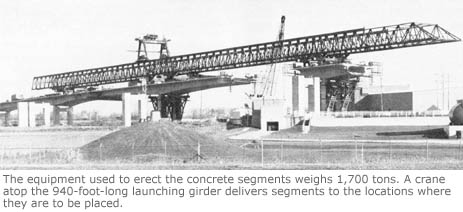
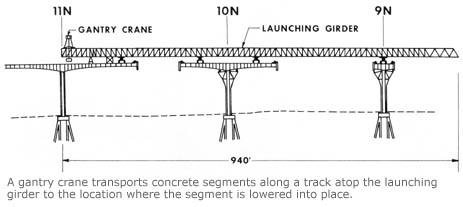
MATCH CASTING OF BRIDGE SEGMENTS
For precast segments, each individual piece is cast against its ultimate mate on the structure, a process called "match-casting." It assures thatthe pieces will fit perfectly when they are placed together on the bridge.
The segments at Zilwaukee were constructed at a specially designed casting plant at the bridge site. Five sets of casting forms inside the building and one set outside were specially tailored to cast the 1,592 segments needed to complete the bridge. The last one was cast in late 1986.
The segments were cast of specially designed concrete which is one-third stronger than that usually specified by MDOT for bridge decks. Segments are 73.5 feet wide and either eight feet or 12 feet long. They weigh between 120 and 160 tons.
The Department followed rigid procedures for quality control during the fabrication of the segments. Each one was closely inspected by a specially trained, four-person team to ensure that they met predetermined standards before being installed.
[Image: The bridge takes shape. Ground view shows massive dimensions of the new bridge as segments are erected one against another and are post-tensioned with many steel cables to form the decks.]
CONSTRUCTION
Construction begins by placing two segments directly atop a bridge pier, or pillar. A match-cast segment is attached to one side of that pier group and another is attached to the opposite side. This balanced group of four segments is then pulled together with high-strength steel cables, also called tendons, to form a solid unit.
It is the cables that hold all the segments in compression. At Zilwaukee, each cable is about the size of a man's wrist. Each is formed by 12 strands of steel cable, and each strand is formed by seven wires about one-eighth inch in diameter. There will be about 27,000 miles of eighth-inch wire in the completed 1.5-mile-long bridge.
Each cable is stretched with hydraulic jacks, stressed to nearly 200 tons, and then locked in place with tapered steel wedges, a process called post-tensioning.
When the balanced group of four segments is in place, a segment is again added to one end of the completed group, and then a balancing segment is fixed to the opposite end. The two new segments then are stressed to the group to create a solid unit, six segments long.
This process is repeated until the entire span is closed. When two adjacent spans are complete, the last segment is cast in place to join the spans. Many more steel tendons are stressed at this time to make the two spans act as a continuous bridge.
As an aid in joining each precast piece to its mate, high-strength epoxy is spread on both matching faces before they are brought together. The primary purpose of the epoxy is to act as an environmental seal of the joint between the segments. It helps prevent water and roadway contaminants from leaking into the bridge itself. It also lubricates the segment faces as they come together and fills the tiny imperfections in the faces. When completely cured, the expoxy is stronger than the concrete segments which it joins.
Cables in the bridge run through galvanized steel ducts that have been cast into each segment. After a bridge span is complete and construction has progressed down the bridge, all the ducts in the completed span are filled with cement grout under high pressure. The grout cures to become concrete, forming another layer of protection for the steel cables.
Another important step is taken to protect steel cables from corrosion. MDOT's policy requires concrete cracks be repaired if they are larger than .004 inches (about the thickness of a human hair). High pressure injection of an epoxy resin makes the repaired area stronger than the concrete was originally and prevents water seepage. Cracks smaller than .004 inches cannot effectively be injected or sealed.
THE ERECTION MACHINERY
On precast segmental bridges, the concrete segments must be delivered to the bridge and held in place while the epoxy is applied and the cables are installed. At Zilwaukee, these jobs are accomplished by two specially designed machines made for that particular project.
Segments are transported from the fabricating plant to the bridge by a long flatbed truck and trailer. Because it would be virtually impossible to turn the 70-foot trailer around on the 73-foot wide bridges, the trailer can be pulled from either end. The tractor simply delivers the segment onto the bridge, unhooks from the front end of the trailer, hooks to the back end and drives directly off.
The tractor and trailer combined weigh 102 tons. The largest segments on the job weigh 160 tons, so the loaded unit can weigh up to 262 tons, more than six times as much as a fully-loaded standard 18-wheel, 40-ton truck.
The segments are erected by a massive piece of machinery called a launching girder. The device is 940 feet long and can easily bridge across the longest two spans of the bridge simultaneously. It stands on its own steel legs and can roll across these legs when necessary to move to a new position as the construction proceeds. A track-mounted crane atop the launching girder picks up the segments from the truck and delivers them to the location where they are to be erected. The total launching girder apparatus weighs 1,700 tons.
The weight of the launching girder, combined with the truck carrying a concrete segment onto the bridge, is the equivalent of 49 fully-loaded auto transporter trucks weighing 40 tons each. Thus, the new bridge is subjected every day to far heavier weights than it will ever experience after it is opened to traffic.
Next: Section 4: The Accident
Back to: Section 2: Background
Back to: Table of Contents