The Zilwaukee Bridge: From the Beginning
The following pages reproduce a 1987 report issued by the Michigan Department of Transportation in response to public concerns about the safety of the Zilwaukee Bridge, then nearing completion. The text here is reproduced word-for-word from the original report and no alterations—grammatical or otherwise—have been made. |
RESUMING CONSTRUCTION
Desingers of the bridge and MDOT engineers and administrators involved in its construction have taken extensive measures to assure its strength and safety.
Perhaps the most dramatic test of the bridge's stability occurs each time a new concrete segment is attached during construction. While it is being built, the bridge carries loads far greater than it will carry after it is opened to traffic.
The tractor/trailer vehicle transporting concrete segments onto the bridge each day weighs up to 262 tons when loaded. The launching girder apparatus used to erect the segments weighs 1,700 tons. The combined weight of this equipment is the same as 49 fully loaded standard 18-wheel semi-trucks and trailers. To create the same load on the bridge in the same space, the 49 trucks would be lined up bumper-to-bumper across four lanes.
Another important point: When completed, the bridge will be much stronger than it is at any time during construction because all spans will be permanently joined with steel cables.
Specifications for the bridge deck segments require concrete strength of 6,000 pounds per square inch (psi), compared to 4,500 psi for other bridges on the state highway system. The average strength of the concrete is actually 10 percent higher than 6,000 psi and runs as high was 7,700 psi.
Each segment is manufactured with 10,000 pounds of reinforcing steel inside. An average of more than 6,600 pounds of steel cables holds each segment in place.
There are more than 4,000 miles of post-tensioned steel cable in the 1.5-mile-long bridge. To protect them from corrosion, all the high strength, post-tensioned steel cables inside the bridge are completely encased in concrete.
A special covering of latex-modified concrete will be placed on the bridge deck, providing a further protection against corrosion. A non-corrosive salt substitute—calcium magnesium acetate—will be used for snow and ice control on the bridge decks.
The epoxy used as sealant at the segment joints is fireproof, and, when it hardens, is stronger than concrete.
MDOT is developing an intensive maintenance plan for the bridge for use once it is opened to traffic. It will be based on a detailed maintenance manual of the type that has been developed for other major bridges, including the Mackinac Bridge, International Bridge and the Blue Water Bridge.
MDOT will hire an expert consultant to do a maintenance inspection on the bridge at least every other year. In addition, a special MDOT design and engineering team will make frequent additional inspections.
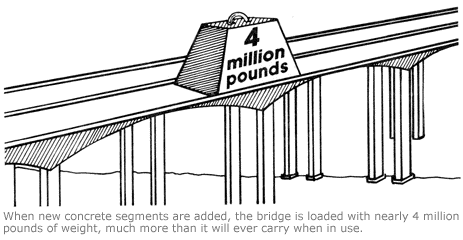
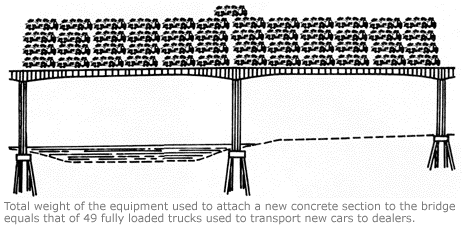
QUESTIONING SAFETY
Late in 1986, a consulting engineer hired by the Detroit News spent what he reported as "a few hours" at the bridge and concluded erroneously that spalling cracks were caused by poorly constructed deck segments with the faces that were not well matched. He did not confer with any of the engineers or consultants working full time at the bridge. The report of his opinion, published in the newspaper, called into question the safety of the bridge and its structural integrity.
CONCRETE SEGMENTS
Meeting exacting specifications in casting the segments is essential to maintain the bridge's structural soundness. The department follows rigid procedures for quality control during the fabrication of the 1.592 steel-reinforced concrete segments required to complete the bridge.
To accomplish this, the concrete segments are made in the same order they are placed on the bridge. They are "match cast," one against the other, so that a finished segment is lined up against the forms for the next segment. Once face of the completed segment becomes the form for the next segment. This type of casting provides for the exacting fit that is required for this type of bridge construction.
All of the bridge segments are closely inspected by a specially-trained, four-person team to ensure they meet predetermined standards before they are installed. Those that do not meet the standards receive additional work until the standards are met. If our standards cannot be met, the segments are destroyed. Before installation, all of the segments are sandblasted to improve the surfaces and provide a closer fit during installation.
The "spalls," or circular surface cracks were caused by water trapped in the bridge segments which froze during the winter of 1985-86, not by poorly constructed segments.
It is important to understand that the spalling does not affect the strength of the bridge. However, spalling problems need to be repaired, and those repairs are being made.
MDOT has long been engaged in the test that was recommended by the newspaper's engineer to assure structural soundness (see next chapter). The Department is continually testing materials, construction techniques and the structure itself, and this process has been intensified since the accident that occurred on the bridge more than four years ago. Scores of sophisiticated techniques are used on site and in the laboratories of MDOT and the contractor to assure the structural integrity of the bridge as construction takes place.
OTHER REVIEWS AND OPTIONS
In his review of the bridge, Walter Podolny Jr., a structural engineer for the Federal Highway Administration, said: "The MDOT has, in my opinion, initiated proper repair procedures, and I do not consider that the structural integrity of the structure has been compromised..."
In reviewing the engineer's letter to the Detroit News, MDOT's engineering consultants, Howard Needles, Tammen and Bergendoff, concluded: "...the evidence does not support [his] opinions and, therefore, no credible reason to question the structure has been advanced."
The U.S. General Accounting Office has begun an investigation which will be made as work on the bridge proceeds. Its report will be released later.
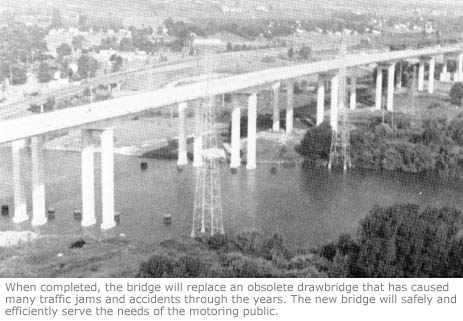
Next: Section 9: Testing and Inspections
Back to: Section 7: Resuming Construction
Back to: Table of Contents